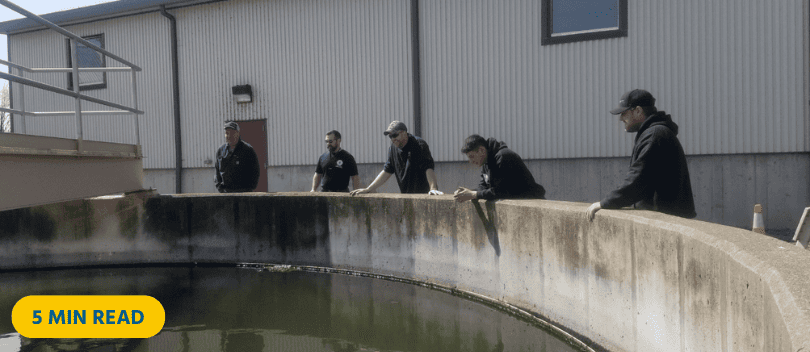
5 Ways Rio Software Has Improved Penn Yan Facility’s Operations
In our latest webinar, we chatted with Yvonne Tucker, the Chief Operator at the Village of Penn Wastewater Treatment Plant in New York, to discuss how they get ahead during times of increasingly scrutinized budgets and increased chemical costs.
The wastewater treatment plant digitized operations and compliance with cloud software and remote mobile technology to enhance their facility's performance and visibility for easier compliance reporting, faster round hand-offs, and optimized pump and asset up-time.
Click here to watch the full webinar recording. This article highlights the 5 key ways that Rio has helped the facility optimize their operations and compliance.
1. Identifying Areas for Cost Savings
According to Yvonne, Rio’s ability to identify trends has enabled the utility to identify & respond faster to issues, allowing them to save costs. One of the issues, she says, was with one of their pumps. “It was a new pump station. And we were tracking the pump hours on with Rio. And as soon as we saw that there was a like a trend difference in the pump hours, we were able to identify that there was an issue with that pump station and we got the manufacturer's rep to come right out and correct that so that there wasn't any damage or further damage to that pump station, which was great.
So that that was a cost savings. And we also trend or track our chemical feed system with Rio. So we can know on a daily basis what we're utilizing and compare that to a week ago, two weeks ago or seasonally in the last year compared to this year. And that helps us keep tabs on our cost of chemicals, which everyone here who buys any chemicals knows the price has really gone high over the past two years.”
2. Unlocking Proactive Response
In regards to how Rio has impacted the facility’s response time, Yvonne says, “I don't have to really think about where our effluent parameters are, are trending or whatever the setting up warning limits and alarm limits. It's pretty awesome because a notification comes right out and lets me know.
I don't have to continuously run into the laboratory and ask, you know, what, what's our results on this? Or how is this happening? Because it automatically notifies me. And so I don't have to worry about a lot of that anymore. It’s great.”
3. Providing Visibility into Facility Performance
According to Yvonne, the plant is still working to finesse their data management.
“However,” she says, “We are able to see immediate deviations from normal values for any given parameter. And that translates into that early notification I just mentioned from whether it be process upsets or equipment malfunctions. And our plan is to integrate our laboratory analytical equipment so that as we are actually performing the analysis, the results are being shared or uploaded into Rio.
And then Rio allows us to easily set those either permit limits or warning limits that send us notifications. So this allows us to be completely in the know and we don't have to think about it. We don't have to spend time reviewing the lab data when there's so many other demands on our time.”
4. Simplified & Faster Reporting
Prior to putting a centralized data management system in place, many of our current customers have relied on Excel, benchsheets, and notepads. Penn Yan's facility found that with spreadsheets, they were repeating manual data input processes and losing valuable time chasing after that data when it came time for reporting or presenting findings to stakeholders.
“With Excel, we would have to go to multiple workbooks and sheets and extrapolate that data, cut and paste, and sometimes even just print it out and retype it in to accomplish what we needed to do. Now I am realizing hours of time savings.
it's literally this easy. I open up Rio, I click on reports, I click on the netDMR, save it into my folder. I can do a quick review of the results just to make sure that there are no issues. And I'm ready for upload into the netDMR. It's literally that fast and I'm so grateful for that.”
Continue Learning
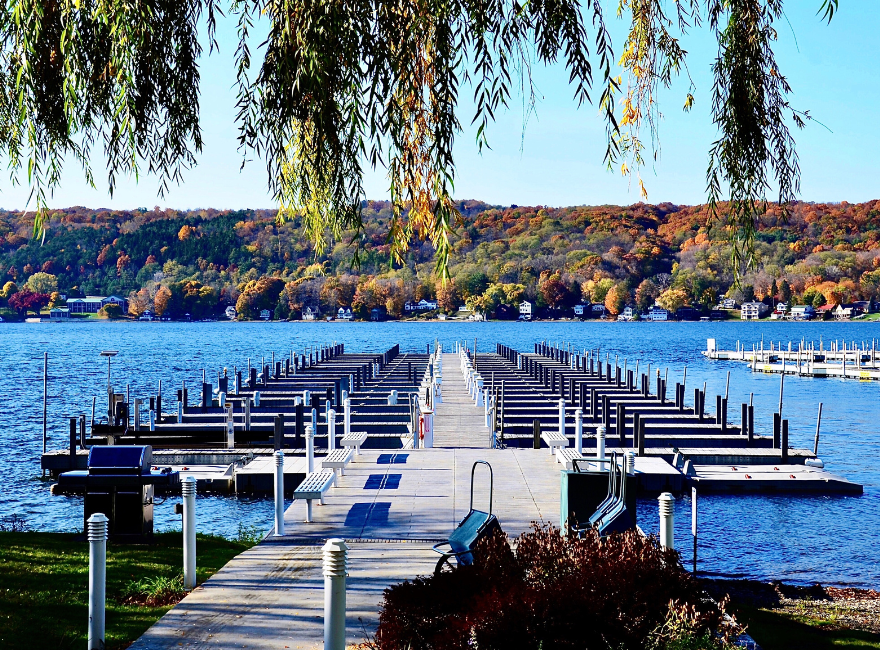
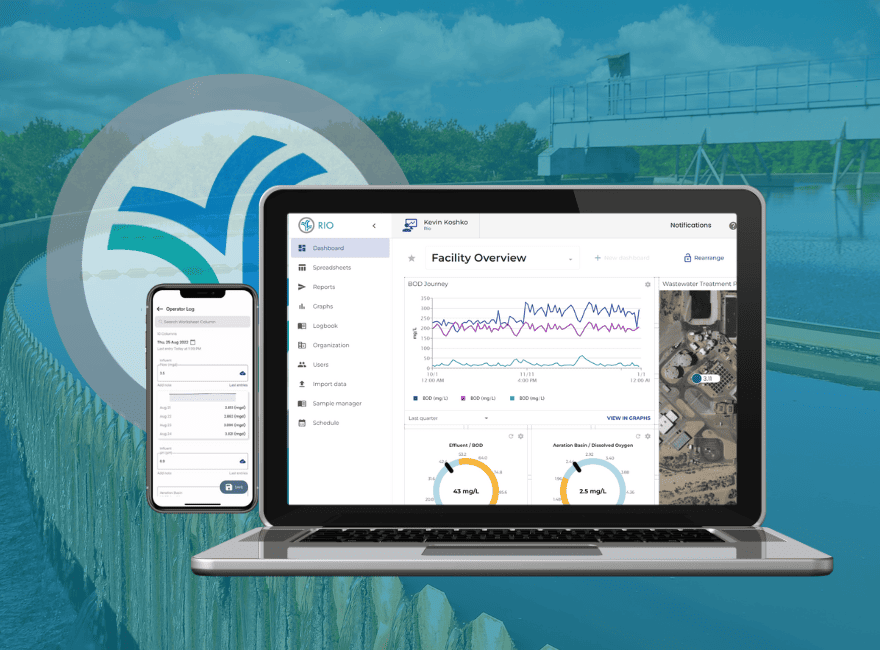
5. Data Visualization for Communication With Stakeholders
Throughout the webinar, Yvonne spoke to how having a centralized data management system in place has helped the facility overcome their unique challenges, especially in its ability to visualize and contextualize outliers.
“We have a categorical industrial user and organically we were being overloaded pretty routinely. We were in significant noncompliance, and we were under a consent order.
And through Rio I was very easily could graph how quickly the devices would gain weight or shed weight and showing a board member a picture or a graph means so much more than me standing up there repeating that this industry is impacting us.
It was a game changer for me because they actually started to see like, wow, this is actually happening. So it's been wonderful for me to be able to utilize that just to communicate to the decision makers the real issues that we have.”
6. Bonus: Knowledge Sharing & Retention
In speaking to how Rio has empowered their operations, Yvonne says, "So I have been here at the Penn Yan Wastewater Treatment Plant for about five and a half years. And when I started here, there was a workforce of four individuals, plus myself. And all four of those individuals retired within a three year span. So they had served their 20 and 30 years and all retired within a three year window.
The new people that we have hired is a younger generation and they are much more adaptable to the digital universe. They pick up the use of the dashboards and use their smartphones for everything with Rio. The mobile app is an ideal tool to allow us to use the tablet for remote work as well as our daily rounds.
With relatively younger staff, they kind of demand that access to the digital...We're starting them off using Rio and they're very accepting of it because they're so used to the digital universe.
Learn More About Penn Yan Village WWTP
Penn Yan Village's Wastewater Treatment Plant is located on the north end of Keuka Lake in the state of New York. They're in the heart of the Finger Lakes region and serve a population of around 5000 people and many of the challenges they face and are no different from any other treatment plant. Download the full case study to learn more about the Village of Penn Yan's WWTP and how they've leveraged data management to optimize their operations.
Find Your Partner in Change Management
As utilities progress on their digital transformation journey, one of the main challenges they face is resistance to change.
Technology partners can help organizations guide their change management strategies to ensure the success of any new technology projects. While every utility is unique, many of the challenges are similar: legacy systems, data silos, lack of resources, etc.
Experienced technology partners like Aquatic Informatics have seen it all before. We can help you achieve streamlined quality control for your facility.
Get in touch to discuss your water data projects, check out our upcoming product demo, or schedule a personalized demo of our platforms.