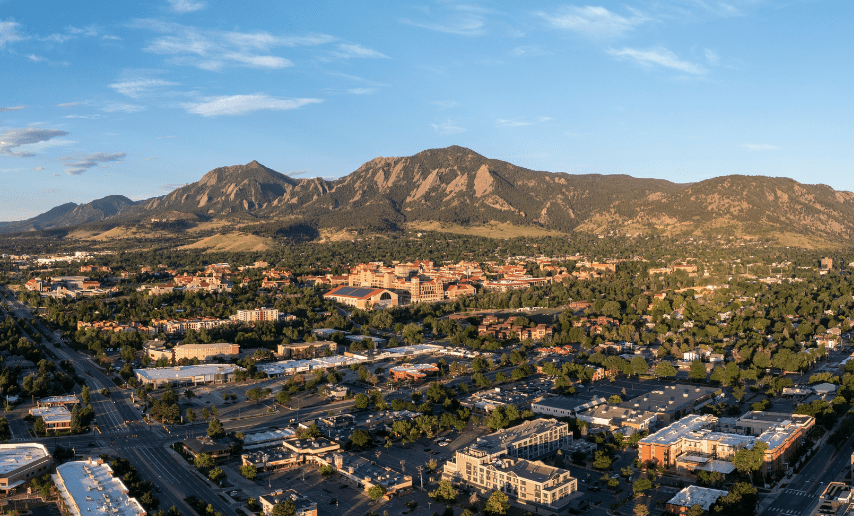
Budgetary pressure on water utilities continues to grow due to factors such as new infrastructure demands, increasing regulatory compliance requirements, and the scarcity or declining quality of source water. Some utilities are addressing this challenge by reducing their operating costs through the capture and analysis of operations data, and leveraging this information to make data-driven decisions around optimization, efficiency and time-saving opportunities.
In the city of Boulder, Colorado, process optimization specialists are using an information management system to streamline operations, simplify reporting, and manage significant cost-savings projects. The City of Boulder manages two water treatment facilities: Betasso Water Treatment Facility and Boulder Reservoir Water Treatment Facility. In addition to the two water treatment facilities, Boulder also manages a wastewater treatment facility, the 75th Street Wastewater Treatment Facility.
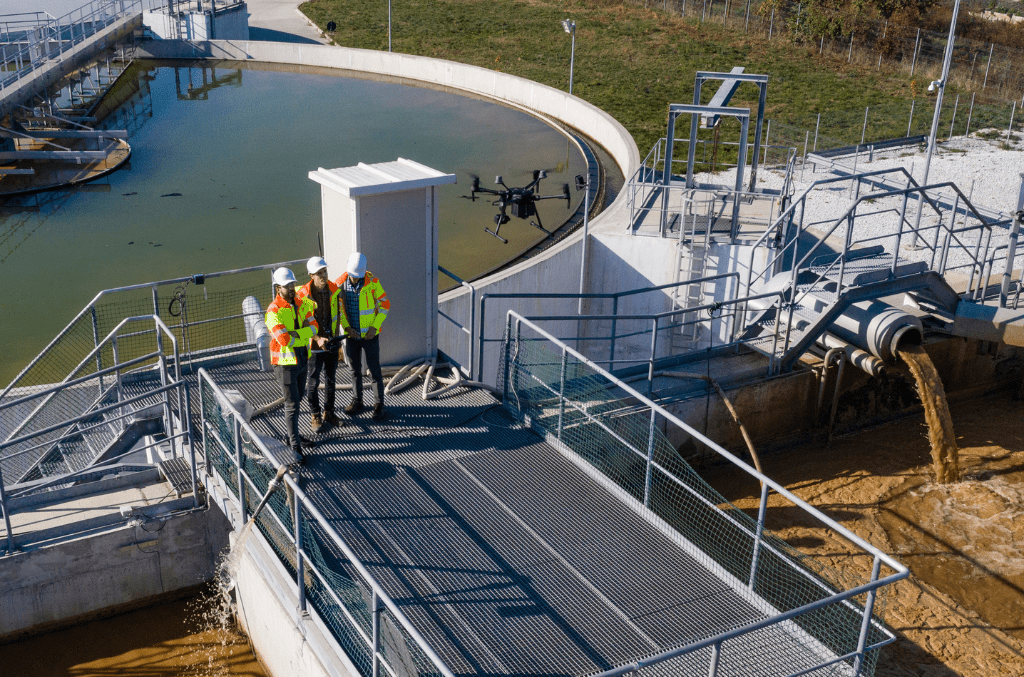
Sorting through the maze of data in a large utility
In the past, the drinking water facilities were tracking all of their data through the use of Laboratory Information Management System (LIMS) software, but it was challenging to manage information — especially non-lab data. Vicki Jones, Process Optimization Specialist said, “It was very difficult to pull data out of the system with the application or run analysis needed to make operational decisions.” Easy access and usability was a key requirement for operators. As a regulated community water system, Boulder’s treatment facilities were required to provide detailed reports on the process, performance, and end results that flow from the facilities. The only reports the city wrote from the old database were the state turbidity, chlorine, and fluoride reports. This was a very time-consuming and cumbersome process. “The operators used to literally manually enter data into the state’s template,” says Jones.
Additionally, the facilities did not have an effective method to monitor operational processes. Operational effectiveness was set by routine and habit. Although the facilities had a SCADA system and LIMS, their ability to combine the information to see trends over time was limited. Jones said, “There were no summary reports to look at changes over time and quickly evaluate optimization and efficiency gains.”
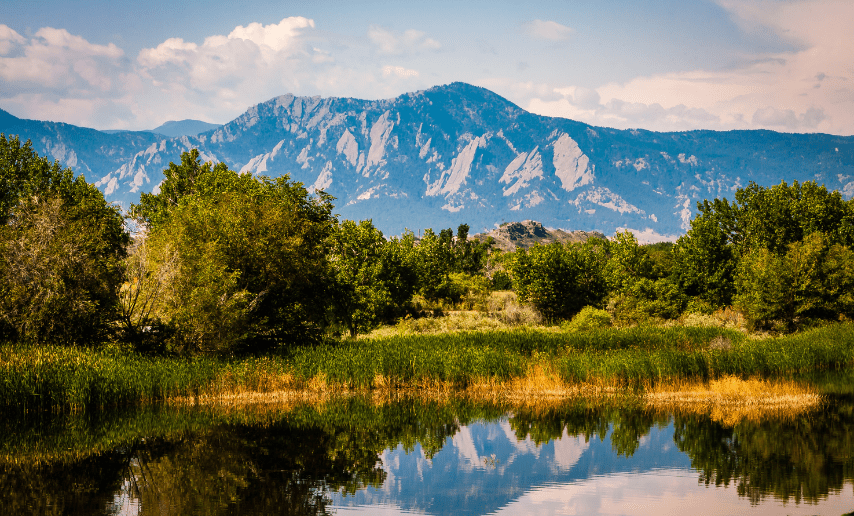
Information management system implementation
The past situation left Boulder with limited ability to use their information to make process optimization decisions because they could not create charts and reports that illustrated correlations, trends, and comparisons between measurements. Also, their regulatory reporting process took a significant amount of time away from operators that could have been spent making strategic treatment decisions.
To address these concerns, Boulder turned to the use of an early version of WIMS. The result was a central database for optimization specialists and operation supervisors to track and manipulate data to drive efficiency. Through an ongoing discovery of WIMS’ capabilities and tools, these associates have gained confidence in the data and reporting and are taking a new approach to optimize operations and reduce cost. A key factor in choosing to implement WIMS was that it was a commercial-level solution that was easy to use and maintain. Today operators, managers, and other key personnel have personalized dashboards that are set to individual security levels and show customized data sets that are relevant to the user. WIMS made the data meaningful.
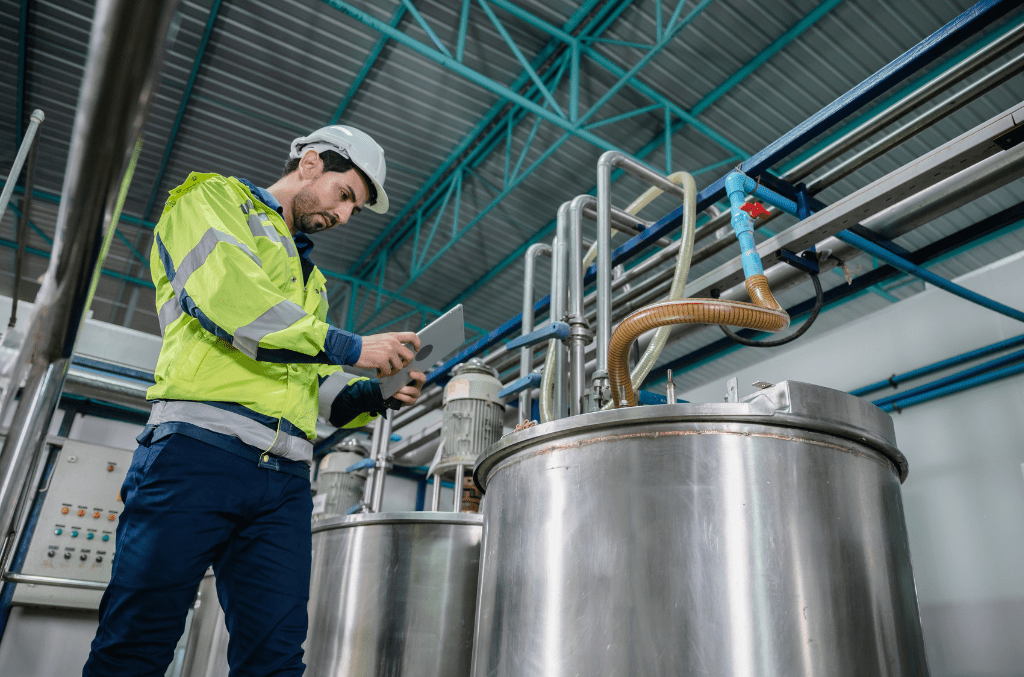
Decreasing time spent & increasing confidence in data analysis and reporting
The drinking water facilities in Boulder can now pull all information from one single source, WIMS, in order to create reports. Using the capabilities of WIMS they have developed data entry forms to look exactly like the operator’s bench sheets. Once the data is in the system it can easily and automatically be inserted into the exact format of the state report, effectively reducing the entry time on the report from 8 to 10 hours a month to about 15 minutes.
facility personnel are also routinely asking for more data because it is now trustworthy and readily available. They are able to make more data-driven decisions in their roles. Data is now mostly entered automatically supporting optimization and summary reports that are mailed automatically every Monday morning to key personnel.
Any concerns about outliers in the data can be handled quickly by operators who can identify the four-hour window for each data point, make necessary changes, comment on the change and re-run the report all in a matter of minutes. Finding these types of problems used to eat up days of the operators’ time and resources. Now it takes a couple of hours.
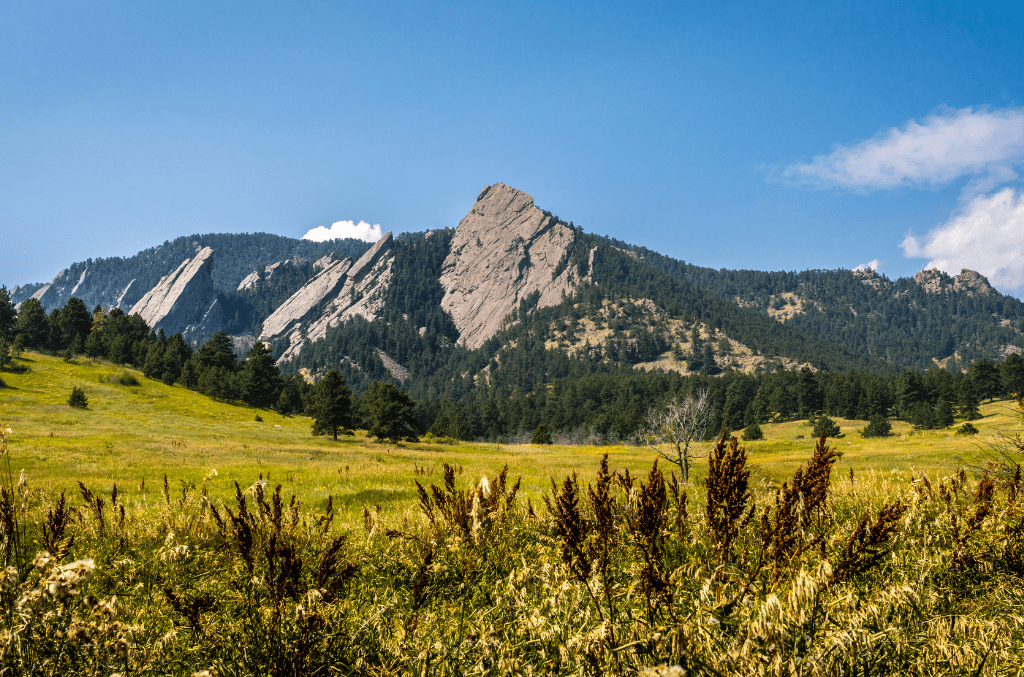
Optimizing operations and reducing costs
Niall Stewart, Process Optimization Specialist at Betasso, believes that by using WIMS to look at long-term correlations between trends they will be able to determine the cause of the sudden residuals and save the $200,000 a year in hauling costs by dewatering the residuals. “We will be using WIMS to track all the tweaks that we do in the facility,” he said. Jones predicted success with the tools and the project, “By evaluating and focusing on this data, I am anticipating they will be able to come up with a fix that’s going to save that recent increase in expenditure.”
Utilities across the country will continue to face budgetary pressure. Utilities such as Boulder will continue to hedge against this issue by looking for solutions that help to reduce costs while maintaining or improving quality. By watching trend and correlation information that is available in information management software, utilities can drive for continual improvement — making changes, piloting processes, monitoring the results, and building on their successes.
In addition to the cost savings, Boulder is ultimately producing better product through their use of WIMS, specifically lowering disinfection byproducts, lower turbidity, and a more stable distribution system. Dedicated to their mission, Jones summarized, “The gain is you are getting better quality water coming out of the facility.”